Redesigned Cystoscope Handle
BME 673 (Advanced Design and Manufacturing): January 2023 - May 2023
This project was one of two main projects I worked on as a part of the BME 673 design course. The focus was to redesign the rigid cystoscope handle to be less "scary" for patients undergoing cystoscopy. Working on this project taught me a lot about what to consider when designing a medical device, or anything in general. Sketches are your friend, consider how the medical device is actually going to be made/manufactured as you design, consider safety of device with tools such as finite element analysis, and don't be afraid to take things apart to understand how they work and can be improved.
The Problem
I'll be frank, the rigid cystoscope looks a bit like a medieval torture device... especially since it is supposed to enter the urethra.
​
To begin designing a handle for the cystoscope that would be more approachable for patients, I started with a mood board, based around words I wanted to describe a medical device that would be used on an awake patient. This led to sketches of a handle idea.


Mood board based on the key words: soft, approachable, simple, warm. The main features I noticed and decided to incorporate into my design was a circular/bulbous shape, no sharp edges, textured surface, and white and brown/dark colors.​

Sketch on the right shows third angle projections of cystoscope handle design as well as a perspective view of device. Device constraints:
-
Must accommodate securely mount and protect the widget (i.e. the photon engine)
-
Must provide an in/out water connection (think luer-lock IV tubing)
-
Must provide provision to control water inflow and outflow
-
Must accommodate 24F sheath, ~20cm in length (circular is fine)
-
Must suit left or right handed use
-
Incorporate electrical connection
Manufacture and Safety Design Considerations
The cystoscope handle was designed on fusion360. During design, I decided that the device would theoretically be injection molded out of some sort of plastic, maybe Bayblend or ABS. Injection molding would allow for fast and cheap manufacture of the device, and it would allow a lot of freedom in designing the device parts. As such, I decided to design my cystoscope handle in two parts, separated by a middle split line. The parts would be held together through screw bosses. Below is the draft analysis of the left component of the device.

After designing the cystoscope handle, I dropped it in a virtual simulation for Finite Element Analysis (FEA). I wanted to test certain areas of the device that I thought had the greatest potential for failure during use. For the FEA to the right and below, I simulated the stress that would occur when a force is placed downward at the tip of the cystoscope sheath, taking into account gravity. The right image shows a safety factor above 1 and the image below shows stress distributions experienced by the device.


Device Visualizations
Below are external and internal renders of the final cystoscope CAD design, as well as a turntable animation of the device. I also photoshopped the device to give a visual demonstration of what it would look like in use in an actual clinical setting.
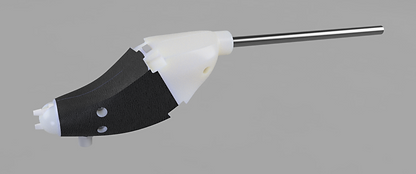
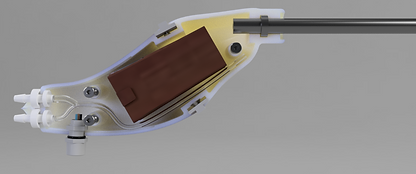
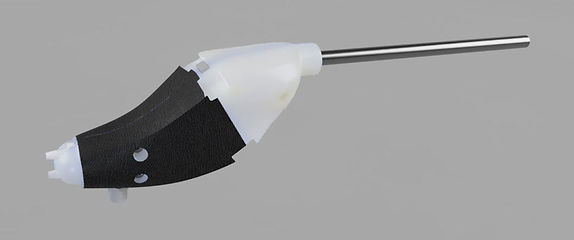